Exploring 3D And 2.5D IC Packaging
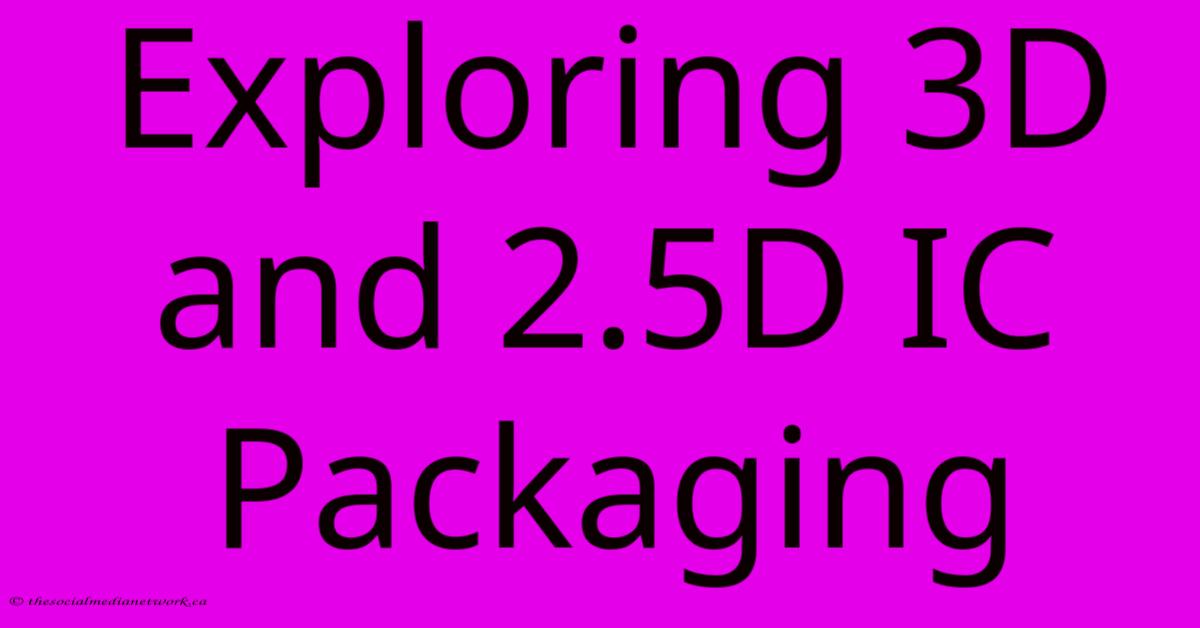
Discover more detailed and exciting information on our website. Click the link below to start your adventure: Visit Best Website meltwatermedia.ca. Don't miss out!
Table of Contents
Exploring 3D and 2.5D IC Packaging: A Revolution in Semiconductor Technology
The relentless pursuit of smaller, faster, and more energy-efficient electronics has driven significant advancements in integrated circuit (IC) packaging. Traditional 2D packaging is reaching its limits, leading to the rise of 3D and 2.5D IC packaging as revolutionary solutions. This article explores the nuances of these advanced packaging techniques, their benefits, and their impact on the future of electronics.
Understanding the Basics: 2D vs. 2.5D vs. 3D Packaging
Before diving into the specifics, let's establish a clear understanding of the fundamental differences:
-
2D Packaging (Planar): This is the traditional method, where components are arranged on a single plane. While simple and cost-effective, it suffers from limitations in terms of interconnect density and performance.
-
2.5D Packaging (Interposer-based): This bridges the gap between 2D and 3D. It utilizes an interposer, a substrate with high-density interconnects, to connect multiple dies (individual chips). This significantly improves signal routing and reduces signal delays compared to 2D packaging. Think of it as a sophisticated "highway" connecting different chips.
-
3D Packaging (Through-Silicon Vias (TSVs)): This represents the pinnacle of integration. Dies are stacked vertically, connected by TSVs – tiny vertical vias drilled through the silicon. This enables significantly higher density and shorter interconnects than 2.5D, leading to improved performance and power efficiency.
Advantages of 3D and 2.5D IC Packaging
The adoption of 3D and 2.5D packaging offers several compelling advantages:
-
Increased Performance: Shorter interconnect lengths drastically reduce signal latency and power consumption, resulting in faster and more efficient systems. This is crucial for applications demanding high speed and low power, such as mobile devices and high-performance computing.
-
Higher Density: These advanced techniques allow for a significantly greater number of components within the same physical space. This is particularly beneficial in shrinking form factors, like smartphones and wearable devices.
-
Improved Power Efficiency: Reduced signal delays and lower power consumption per interconnect contribute to overall system power savings. This is essential for extending battery life in mobile devices and reducing energy costs in data centers.
-
Enhanced Functionality: By integrating multiple dies, 3D and 2.5D packaging enable the creation of systems with more complex functionalities and capabilities. This opens doors to innovative applications in various sectors.
Applications of 3D and 2.5D IC Packaging
These advanced packaging technologies are rapidly finding applications across a broad range of industries:
-
High-Performance Computing (HPC): 3D and 2.5D packaging are vital for creating powerful processors and accelerators required for demanding HPC workloads.
-
Artificial Intelligence (AI): The enhanced performance and power efficiency are critical for AI applications, including machine learning and deep learning.
-
Mobile Devices: Smaller, faster, and more energy-efficient chips are essential for smartphones, tablets, and other mobile devices.
-
Automotive: Advanced driver-assistance systems (ADAS) and autonomous driving rely on high-performance, reliable electronics made possible by 3D and 2.5D packaging.
-
Networking: High-speed data transmission requires advanced packaging solutions to handle the increasing bandwidth demands.
Challenges and Future Trends
Despite its advantages, 3D and 2.5D packaging face several challenges:
-
High Manufacturing Costs: The complexity of these techniques leads to higher manufacturing costs compared to traditional 2D packaging.
-
Thermal Management: The high density of components requires careful thermal management to prevent overheating and ensure reliability.
-
Testing and Reliability: Testing and ensuring the reliability of these complex systems pose significant challenges.
Future trends in 3D and 2.5D packaging include:
-
Further miniaturization: Continuous advancements will lead to even smaller and more densely packed chips.
-
Integration of new materials: The exploration of new materials with improved thermal and electrical properties will enhance performance and reliability.
-
Advanced interconnect technologies: Research into novel interconnect technologies will improve signal integrity and reduce power consumption.
Conclusion
3D and 2.5D IC packaging represent a significant leap forward in semiconductor technology. By overcoming the limitations of traditional 2D packaging, these techniques unlock unprecedented levels of performance, density, and power efficiency. While challenges remain, the ongoing advancements in this field promise to shape the future of electronics, driving innovation across diverse industries and enabling the development of more powerful, energy-efficient, and sophisticated electronic devices.
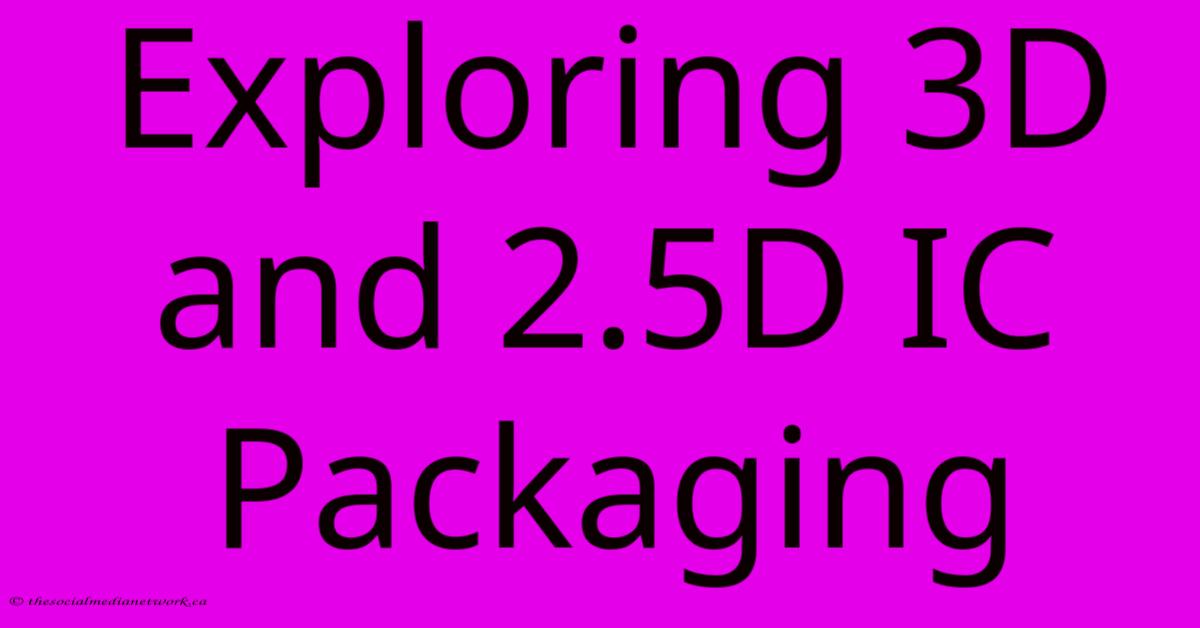
Thank you for visiting our website wich cover about Exploring 3D And 2.5D IC Packaging. We hope the information provided has been useful to you. Feel free to contact us if you have any questions or need further assistance. See you next time and dont miss to bookmark.
Featured Posts
-
Growth Through Loss Kalau Kalah Biarlah Kalah
Nov 30, 2024
-
A330neo New Plane For Malaysia Airlines
Nov 30, 2024
-
Piala Malaysia Sembilan And Terengganu Face Off
Nov 30, 2024
-
Revolutionizing Semiconductor Tech
Nov 30, 2024
-
Global Automotive Cables Market 2024 2033
Nov 30, 2024